From high peaks to distant islands, MB Crusher’s units bring solutions and advantages to any job site
MB Crusher’s headquarters is in Italy, in a town less than 100 kilometers from Venice. Here is where the units are designed and manufactured to then be sent all over the world to those who deal with construction, demolition, road work and earthmoving jobs. From the imposing mountains in Tibet to the Cordillera of the Andes, from the Caribbean to Iceland, from snow-covered Siberia to the deserts of Saudi Arabia, it’s easy to travel around the world with MB Crusher’s units.
They start with high mountains. What makes it difficult to work in these locations? Difficulty to reach the areas, difficulty when transporting materials, it involves expensive costs and workshops are far away.
In Tibet, their customer works in the road construction industry, with a job site at 3800m above sea level, in a remote area with spectacular scenery. Using a BF70.2 crusher bucket, the company crushed road waste, produced material, and reused it as a sub-base for new projects. They obtained logistical and monetary advantages: with MB’s excavator crusher, they’ve eliminated the cost of procuring material for future jobs.
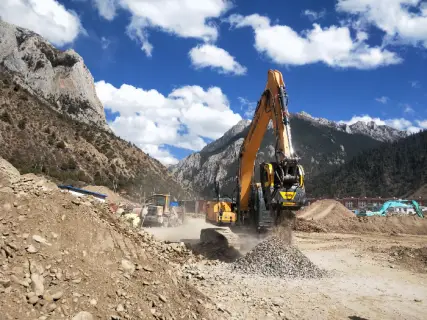
On a different continent, they landed on the Andes, in Perù at about 4000 meters from sea level. In a boron quarry, an MB-S18 screening bucket is sifting coarse material from the fine part. The selected material can be processed easily and faster by the quarry plant.
Their tour continues towards some islands, although far from each other, they share the same challenges: transportation costs and struggle to obtain materials.
In Iceland, among spectacular landscapes dominated by volcanoes and geysers, the MB-S23 screening bucket installed on Caterpillar 345C was the best tool to select large quantities of basalt and immediately obtain filler material that will be used to help construct a hydroelectric plant.
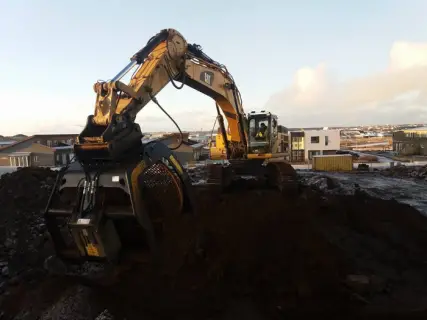
On the other side of the world, in the Caribbean island of Saint Kitts and Nevis, there are two of MB Crusher’s units working on an important redevelopment project in the area. The company in charge of the project needed to renovate the old colonial buildings and rearrange the landscape. The MB-S18 screening bucket was installed on a Caterpillar 320L and separated the dirt from the leaves and twigs: the separated material is reused directly on-site to help maintain the landscape. On the other hand, the BF90.3 crusher bucket is used to crush the Nevis stone, a stone local to the islands and a type of hard granite with volcanic origins. Once crushed, the stone is reused to fill the excavations necessary to construct the buildings and to build the basement for the road network.
High transportation expenses and difficulties finding materials accompany our world tour, even on locations where it’s normal to have extreme temperatures, affecting the job sites.
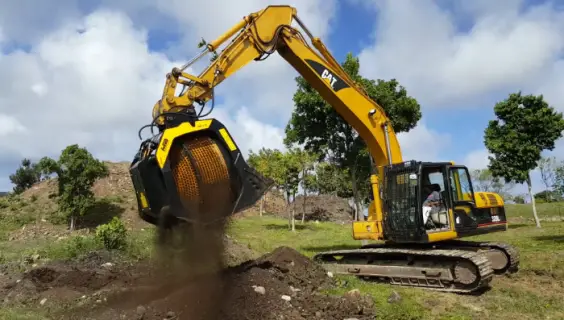
Layers of snow as far as the eye can see and thermometers that read -50°C during the day, almost empty roads, mountains, and forests to cross: thanks to MB Crusher, a company in Siberia brought their BF70.2 crusher bucket and their MB-S14 screening bucket without struggling with transportation costs. With the units, they recycled aggregates of different sizes and reused them to maintain the quarry internal haulage roads.
Something similar happened in Saudi Arabia with its +50°C in the summer surrounded by mountainous and desert locations, is where a BF90.3 crusher bucket is working in the most inaccessible places of a quarry a place that is not reachable by traditional vehicles.
Then there are locations where their exports are appreciated, especially when it comes to excellent wine. Their world tour ends with a visit to Italy and France where MB Crusher’s units are chosen to dispose of the vineyard posts at the end of the harvest season. A great way to save time on the job site which translates into an economic and environmental advantage.