Rabih Hajjar, from CCL, discusses the company’s design and project delivery support for the Eden Roc residential development in Cyprus
With its year-round sunshine and picturesque beaches, Cyprus has long been a popular destination for holidaymakers, second homeowners and retirees. As a result, investment in residential developments on the island has been buoyant, aided by a scheme to grant EU Cypriot passports to those investing in eligible developments. Despite the challenges of COVID-19, the market is expected to bounce back over the coming year and one of the developments poised to take advantage of demand is Eden Roc, a luxury apartment project in Limassol.
Designed by London-based architectural practice, UHA, for Cypriot property development company, Prime Property Group, the Eden Roc development in Limassol is a striking project, designed to stand out in the Cypriot property market with its unusual terraced design. The project is being delivered in two phases. Phase A involves construction of three adjacent residential blocks ranging from five to seven storeys and featuring numerous penthouses with large terraces and private swimming pools. Phase B is a single residential block with eight swimming pools at roof level. Phase B has only recently begun on site but Phase A, constructed to a cantilevered design with the structure stepping in as much as four metres in some locations has now completed.
CCL, the specialist in engineered solutions for structures, has been responsible for designing the post-tensioned slabs for both phases to enable extended spans, provide a solution for the cantilevered design and address the point loads from the rooftop swimming pools. The PT engineering, designed by CCL’s team in Lebanon, has enabled the original design intent, while providing time savings on the programme and reducing the amount of concrete required.
Revising the Design
To create a luxurious open plan playout in the phase A apartments, the properties were designed with large 7-8 metre spans and generous ceiling heights to create a sense of space and allow plenty of natural light. Meanwhile, the phase A buildings are terraced at roof level, reducing the area of each floor as the building rises and creating a cantilever of up to 4m in some locations. Several of the terraces feature swimming pools, creating additional loads for the cover slab in these areas.
It was clear that achieving this design using conventional reinforced concrete (RC) slabs would result in the need for drop beams within the proposed open plan apartments, which would impact on the aesthetics of the properties and the proposed layouts. It would also have required an onerous slab thickness to cope with the planted loads prompted by the cantilevered sections and additional loads from the roof terrace swimming pools.
Detailed Design
Working with load calculations provided by ASD Sotiriou, the CCL team engineered the slabs for the building, adjusting the thickness of the slab, the level of RC reinforcement and the number of PT strands for the areas that are subject to planted loads due to the cantilevers and swimming pools. Typically, this has meant that the slabs could be reduced to 250mm in most areas, increasing to 350mm to support the planted loads in the cantilevered areas and the point loads of the swimming pools. CCL designed each slab individually to deliver the optimum slab thickness for each location, reducing the weight of the structure and the amount of concrete required, while providing sufficient tensile strength for the loads. The transition between slab thicknesses has been incorporated at the interface between internal walls to ensure that it is not perceptible from inside the apartments.
Additional design expertise was required to determine the level of reinforcement needed at the edges of each slab to control the deflections.The experience of the CCL team ensured that the position of reinforcement and PT strands effectively controls the deflections at the slab edge within the exacting tolerance required for the apartments’ floor-to-ceiling windows.
The terrace swimming pools also presented additional challenges, due to the loads created by the large volumes of water. Each of these had to be considered in the context of its individual position and relationship with the structure. Where existing columns were in place to help support the additional loads, or a planted column could be introduced, the slab thickness did not need to be adjusted. Where it was not possible to support the loads with a column or planted column, the CCL team had to calculate the increase in reinforcement and the slab thickness required at critical locations.
Also Read: Gyeongdo Island: New sustainable leisure destination in South Korea
From Design to Construction
The use of PT is still relatively unusual in the Cyprus market and the main contractor for Eden Roc had never built a project with PT before. To ensure that this lack of experience on site was overcome in both the specification and project delivery, the CCL team took an active role in designing the PT specification to aid buildability and worked with the construction team to ensure they were familiar with the system.
CCL specified the company’s XF bonded flat slab system, which connects bare strands, fed through flat ducts. The strands are individually stressed before the ducts are sealed with a cementitious grout.
This specification enabled the contractor to remove the formwork as soon as each slab had been stressed and move on with the programme to the next level, returning to carry out the grouting when the schedule allowed.
To ensure that the contractor had the confidence and competence to install the PT system, CCL invited them to Lebanon to learn about the system. The CCL team also worked with the contractor to select and train the site operatives and supported the construction team on site throughout the installation.
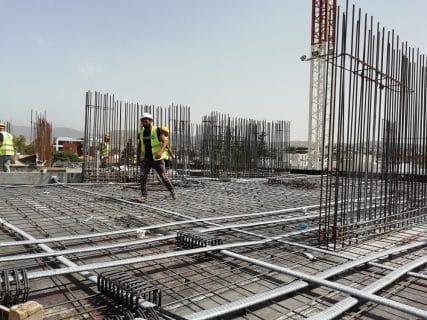
Phase B
The project has now moved on to phase B, which, at 7000m2, is around half the size of phase A, but involves its own specific structural complexities thanks to cantilevers of up to 4m and high periphery loads.
For this phase, the slab thickness will vary between 250mm and 350mm, in order to support planted loads and enable the cantilevers while minimising the need for beams. All the swimming pools for this building will be located on the roof, between the columns, which has necessitated a slab thickness of 350mm for the entire cover slab in response to the loading calculations provided by ASD Sotiriou.
The same XF bonded system from CCL will be used on this phase of the project and CCL will once again provide supervision of the installation.
Stand-out Development
The high-end residential property market in Cyprus is competitive but unusual design and luxury features, like roof-top pools and large, open plan apartments, stand out from the crowd. Thanks to CCL’s collaboration with the design and construction team at Eden Roc, the design intent has been realised and the structural challenges have been overcome to deliver a stand-out development.