The latest technology for contractors building residential houses is 3D printers, which are phenomenal digitization. At one point, the process was used for simple components like printing small elements in the house like plastic tchotchkes.
But the process has taken on a much grander dynamic with the capacity to innovate varied industries from “engineering to autos to construction.” Learn details on 3D printing in construction.
If the technology continues on the patch it’s currently taking, the residential and commercial buildings moving forward into the future won’t need months of preparation but will require mere hours to print.
Some companies are already integrating the process to the delight of the customer base. Let’s look at the technology more in-depth.
What Are The Benefits Of 3D Printing
The 3D printing technique would be better represented as “robot facilities” more so than the traditional “inkjet printer” many consider comparable.
These work using sophisticated software for modeling virtual versions of specific items or, in this case, structures with the vision you create on the screen printed in a physical variation.
This process is referenced as “additive manufacturing.” That implies that the piece is constructed one layer at a time. The concept isn’t a new one. It was implemented in the 1960s with bricklaying, but the “Motor Mason” was a hit then. There are “descendants” echoing its effect today, however.
Architectural models were the first 3D printing performed with construction, but these have since been overtaken by “BIM or Building Information Modeling” as the industry’s method for visualizing a plan.
Creating structures with the technology is relatively new, with this scale of printing dating back to roughly “2006 when contour crafting was introduced.” Click for trends in construction technology.
Constructing structures in a 3D printing context boasts a number of advantages compared to conventional methods. Clients and contractors alike will find these to be:
● The delivery
In the manual process of building a home, many variables can delay the process. That can include weather, clients making changes, contractor errors, and on.
Designing a house allows a prospective homeowner the opportunity and a time period to digitally consider any possible changes before the actual work begins.
Instead of buying materials and building them piece by piece, the contractor can print their digital version. The stick-built home will take months, with the potential for a year or more, depending on the variables.
The 3D printout will be a matter of mere days. Companies in surrounding countries have completed as many as ten homes in as little as a day. The efficacy and speed allow contractors the capacity to take on more projects simultaneously.
● A minimal team
The 3D technology, with its automated technology, allows a minimal team or even a single contractor, perhaps a DIY self-employed individual with less knowledge in the field, to take on projects, even those of a significant size.
You don’t need to be an ace with the jigsaw or feel strong with a tape measure, but if you have some degree of knowledge and ability plus software and equipment access, there’s every possibility for you to construct a structure from scratch alone.
It wouldn’t be unreasonable to consider, at some point in the future, 3D printers would be something anyone could rent, take to a plot of ground they purchase, and print out an entire structure by the time the machine is due back. But not quite yet.
● The options are countless
When a builder attempts to construct intricate designs created by an architect, it can be cumbersome, challenging, expensive, and sometimes impossible to do. When a reputable, forward-thinking builder like Agorus utilizes an architect employing 3D printing technology, creative privilege is endless.
Architects are no longer prohibited by the complexity of the design or what would usually be limited by expense. The professionals can incorporate intricate adornments and elaborate shapes by merely digitally designing and printing what they envision for their clients.
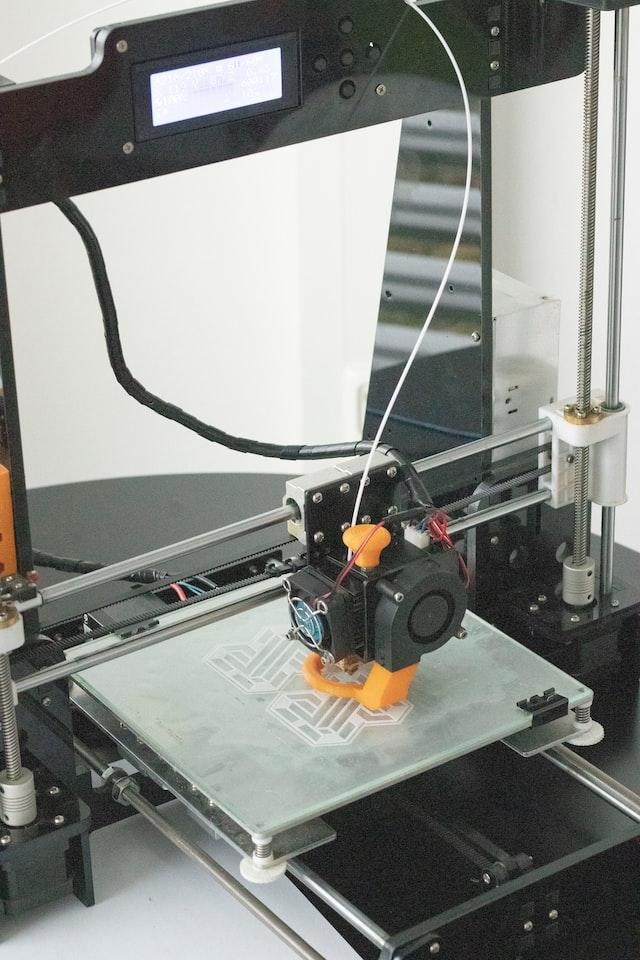
● Recycle, waste less
In the wide world of construction, there is an increasing amount of waste, with the pieces of materials that are not needed for projects or cut off during the building phase just tossed away.
One recycling company indicates, “the construction industry is heading on the path to create waste in the billions by 2025.”
With building using 3D printing technology, the machine prints the precise amount of material necessary for the item or structure, disallowing a significant amount of waste. Plus, where possible, recycled materials are incorporated into each structure.
Final Thought
The capacity to create 3D images for printing to this scale has improved substantially over these last ten years. There is an array of 3D printers for the construction industry.
Contractors have been successful in constructing 3D residential building and commercial structures as well as other construction elements. That doesn’t mean there are no challenges, nor is the process quite ready to be incorporated into broad productivity.
Despite the rough spots, there are many possibilities for innovative technology. Many people were initially skeptical about the internet and look at us now. Down the road, you might be building your own vacation home on the beach in Maui.