The sheet metal fabrication industry is projected to be worth $4.4 billion by 2026 according to bloomberg. This figure is achievable considering sheet metal has become a valuable industrial age material. Initially, it was just iron during the Iron Age. Then came steel, bronze, and all other metals.
Today, all these metals, including copper, tin, nickel, titanium, aluminum, and steel, are combined to fabricate sheet metal. This material has a plethora of uses. But, this article will cover all about sheet metal production in construction. We will see what it is, its application in construction, the advantages of using it, and methods used in sheet metal production.
What Is Sheet Metal Fabrication?
Sheet metal fabrication is the process of creating custom metal products for use in various sectors. The procedure used may include bending and shaping metals to meet a specific design. This process involves manufacturing a product through laser cutting, water jetting, plasma cutting, magnetic brakes, hydraulic brakes, welding, punching, and stamping.
After the above process, a sheet metal product can go through a series of finishes. It can be anodized, pad printed, etched using a later, plated, powder-coated, brushed, liquid painted, or silkscreened.
A manufacturer uses aluminium, copper, titanium, mild steel, stainless steel, steel, and tin to make sheet metals. The products made from this fabrication have extensive uses in the construction industry.
Sheet Metal Fabrication Application in Construction
Sheet metal fabrication is a handy process in construction. The end product can be used in plumbing, roofing, building, fences, staircases, enclosures, and so much more. Sheet metal can also be used as an interior design feature.
The material can be welded into a robust and durable product which is ideal for construction. You can also get a prefabricated metal building. Instead of processing all materials at your construction site, a prefabricated metal building is designed in a setup factory. The products are then shipped to your construction site, ready for erection.
Advantage of Sheet Metal Used in Construction
Sheet metal has several advantages in construction. These include:
1. Low Cost
Sheet metal is readily available. Thus, it is relatively inexpensive. Several factors indicate that sheet metal is a low-cost material. For example, a structure built from the material takes longer before it needs repair. This is because sheet metals are high quality, eliminating the need for constant repair or replacement. It is also versatile, which means it is applicable in various aspects of construction. So, if you have extra material after buying, you could use it elsewhere.
2. Durable
The durability of materials indicates their shelf-life and their lifetime. Sheet metal products can come from Steel, Stainless steel, brass, copper, and other alloys.
All these have unique properties such as strength, ductility, tensile, machinability, toughness, weldability, strength to weight ratio, and more. A manufacturer looks at all these qualities and decides on the best combination to ensure that a client is getting durable sheet metal.
For example, suppose you are looking for sheet metal with corrosion-resistant properties. In that case, the manufacturer combines materials necessary, such as galvanized steel, to ensure the product lasts longer before it ever gets corrupted. They can withstand pests, moisture, sun, and damages from mold or fire.
3. Recyclable
Materials used to manufacture sheet metals are recyclable. Thus, you can reuse sheet metal multiple times in various applications before it can begin to degrade in quality. Scrap metal sheets can be transformed into better products. For example, used metal sheets can be used to make metal art.
Common Sheet Metal Fabrication Methods
Sheet metal services can be achieved in several methods. The most common ones include:
1. Cutting
Cutting is removing unwanted materials off sheet metal. There are several cutting variations, including laser cutting, plasma cutting, and waterjet cutting.
1. Laser Cutting
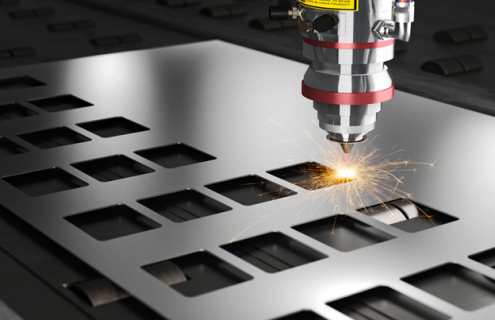
Laser cutting is the process of using various gasses such as nitrogen, carbon dioxide, helium, and oxygen to burn unwanted material off sheet metal until it gets clean edges. The process involves using a jet of gas directed to the area intended to be cut. This jet of gas molten unwanted material and blows it away until you get the desired result.
2. Plasma Cutting
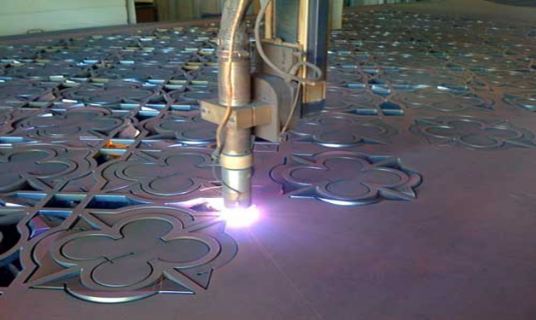
Plasma cutting is a process by a machine in the form of a torch to stream electricity and gas through a small orifice. The streaming is usually fast, resulting in melting and cutting off unwanted material. Plasma cutting is applicable on conductive materials such as aluminum, stainless steel, cast iron, incol, titanium, copper, brass, monel, and mild steel.
3. Waterjet Cutting
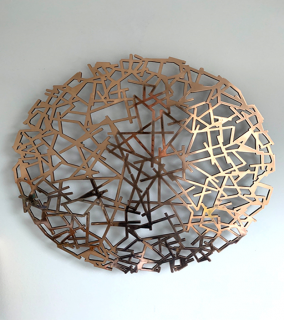
Another way to design sheet metal is waterjet cutting. It involves firing high pressurized water on sheet metal through a nozzle opening made of diamond or ruby. The pressurized water is usually mixed with abrasive material and controlled by a CNC.
4. Punch Press
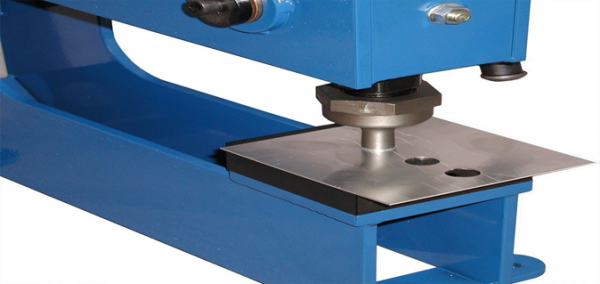
A punch press is an economical version of laser cutting and waterjet cutting. It is used to cut simple patterns. As it is a fast process striking over 100 strokes per minute, the process is used to create parts quickly.
2. Bending
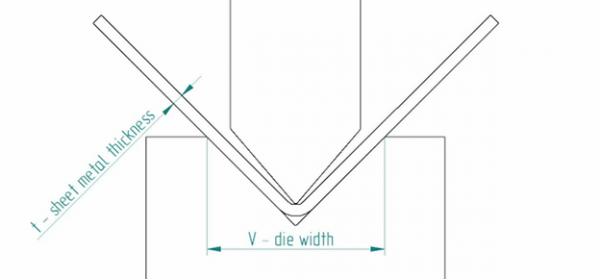
Bending is the process of transforming sheet metal into the desired shape. Various bending instruments are applied to get a product into its ideal form. For example, a die and a punch of any form can be used to create a shape on the sheet metal. A punch and a die come in various shapes and apply pressure to a particular part of the sheet metal to create the desired form.
Final Thoughts
Choosing sheet metal for your construction is just the first step. You also need to identify the purpose of the material and measurement. Then, your manufacturer helps you define the weight of the material, strength, flexibility, cost, and everything involved in manufacturing. Although it doesn’t sound simple, a qualified engineer and his team will prototype your product to desired results.
RapidDirect creates precise, high-quality sheet metal in the shortest time possible. With many years of experience in offering top-notch sheet metal services make us the perfect choice for your business.
This is a great article, thanks for sharing