With the cost of labor increasing across many markets, and recovery from the pandemic at the center of our focus, it’s essential to consider how to improve upon your warehouse operations and efficiencies. Gaining more productivity per hour of labor is more important than ever before.
For most multi channel businesses, inventory is their primary balance sheet asset. Location and slotting control aid you in tracking product within your warehouse and during the order-fulfillment process.
But, what can you do to improve the efficiency of your warehouse operations and reduce costs?
Incentivize through pay
Correctly engineered performance-related incentive payments can bring about the greatest percentage of labor improvements. It is likely that pick and pack forms the majority of your labor-force, so begin there. It’s important, however, to ensure that you’re not paying for any productivity you are already benefiting from or could attain by other means.
Simplify your processes and reduce handling and costs
Since your operation began, have you been implementing new functions over existing ones? Does the order flow and the product flow now crisscross the warehouse floor, no longer making efficient sense?
Taking a fresh look at the steps and physical processes involved in order fulfilment and product flow can transform a warehouse’s efficiencies. Simply put, the less steps required leads to fewer physical handlings, which ultimately equals lower labor costs.
Measure and assess for improvements
Does your warehouse operation manage and capture its critical KPIs (Key Performance Indicators)? Are you aware of your critical productivity and shipped order costs, including costs per line shipped and cost per box? How is it possible to assess and action cost-reduction measures without first understanding the baselines from which to improve? What do returns cost you? What is the cost of a variety of common errors?
Once these baselines are established, then effective feedback can be created to regularly download to staff, both at an individual and departmental level, regarding performance. From a place of clearly defined goals, you can expect higher productivity in response.
Maximize frontline manager efficiencies
Effective leaders understand that it’s all about execution. Their ability to manage all aspects of warehouse fulfillment efficiently can radically affect the operation’s costs, as well as employee morale and the quality of consumer order fulfillment. So, focus on developing more effective managers – what are their unique needs? What other aspects of the business could you expose them to, to deepen their understanding of your customers, your merchandise and your vendors?
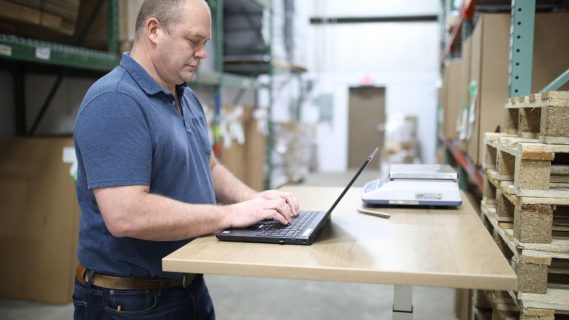
Voice-enabling technology
Voice-enabling technology can be effectively applied to all departments and processes – from shipping, to receiving and returns. This can result in increased productivity and improved inventory control and warehouse efficiencies. Such systems are quick to install, requiring no modifications to your warehouse management system or other IT, they don’t require extensive training, and they can provide a fast Return on Investment (ROI).
There are many other technologies, installations and warehouse and distribution products that are worth investing in for operational improvements, too. As well as all of the necessary safety-related accessories and signage, products like steel barriers and specialized safety stanchions can play a vital role in dispersing and controlling large volumes of workers efficiently to keep operations running smoothly.
Supply chain improvements
Changes to the supply chain can include scheduling inbound orders to better manage the yard and improve upon receiving-dock operations. It’s essential to develop policies for vendor compliance to include terms and conditions of purchasing, item and quality specifications, on-time delivery, importing and routing guidelines, product labelling and packaging, and standards for drop-ship vendors. Push value-added services to the vendors up the supply chain, so that the product is ready to be shipped or put away. These practices reduce labor costs associated with mistake corrections.
Consider using third-party logistics
Utilizing a 3PL (third-party logistics provider) isn’t for everyone, but many do attest to achieving cheaper fulfillments with higher quality. Investing in a 3PL partner can result in capital not being otherwise tied up in new systems and facilities.
For smaller companies, 3PLs can allow management to focus more on merchandising functions and marketing, which is essential to sustainable growth. When the time comes for you to look at increasing storage, warehousing or order throughput, it’s well worth considering third-party logistics as a viable option.
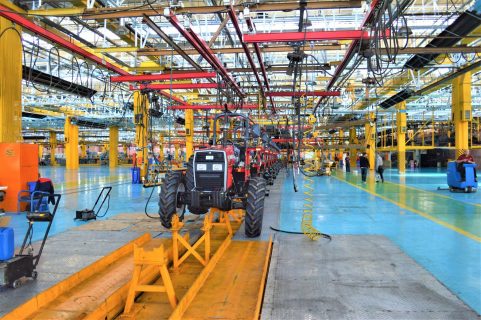
Final thoughts
The most important factor in the ongoing growth and sustainability of your business is to commit to taking a keen interest in continuously seeking to improve your processes.
Great marketers and merchants measure everything regularly to ensure that their promotions and results remain effective and their operations efficiently run. So, assess, formulate a plan, set accountability and objectives for improvement, and regularly review progress.