A company named HyperTunnel has unveiled a proprietary tunnel-spraying robots that it claimed to be “revolutionary infraTech for tunnels”. The unveiling happened during the British Tunnelling Society (BTS) conference and exhibition last week in London.
The importance of HyperTunnel’s underground construction methods are clear to see: there is no going underground until the tunnel is complete, being the safest so far, of lower cost and much faster than traditional methods. Asset owners will really be attracted to the amazing ability HyperTunnel offers, precisely monitoring the behaviour of the whole tunnel over time. Co-chief executive, Steve Jordan added: “We have been delighted by the support and interest in the HyperTunnel approach from around the tunnelling and underground construction industry, and I genuinely believe we have convinced new friends to link to a long overdue new movement in tunnelling, globally.”
Read also: One mile mark completed on Britain’s high speed rail tunnel.
The concept.
HyperTunnel delegates demonstrated how tunnel-spraying robots could convey cartridges of construction chemicals in a horizontal directional drilling (HDD) bore pipes to a tunnel of 3D-print in the ground. From the demonstration, HyperTunnel claimed that the modular approach would be scale up to tunnel repair, building, enlargement and monitoring, making it cheaper, faster and safer. The concept, which is now in advanced testing at different UK sites is to ‘build’ the tunnel digitally first and then send robots to get work done in the ground. With a number of bore pipes as the tunnel’s outline, the the tunnel inside the ground is printed on a 3D.
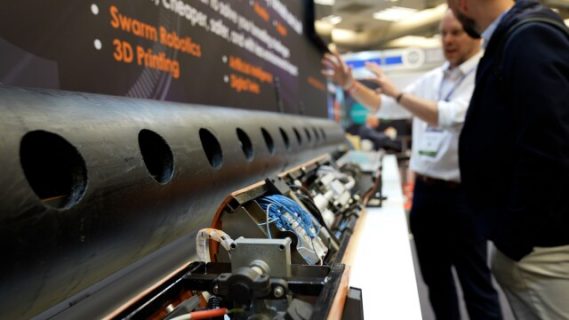
HyperTunnel demonstrated how fleets of mini robots can transport cartridges of construction chemicals through HDD bore pipes to 3D-print a tunnel in the ground using swarm construction techniques
The semi-autonomous robots manoeuvre inside of the bores creating the structural shell of the tunnel with swarming techniques. After disruption of the geology within the shell, spoil is removed using a remote-controlled excavation shield. The ongoing concrete layer can then be sprayed onto the shell and the construction completed, when custom linings is required. Secondary bore pipes are deployed to house monitoring technologies which increase long-term tunnel safety and maintenance.