Lakeside has unveiled a new oxidation ditch, ‘the Closed Loop Reactor (CLR) Process’ which has a basic design that uses a simple racetrack configuration that provides a straight line flow pattern for wastewater between the headworks and the final clarifiers.
The CLR has been featured with a single feed point for raw wastewater and return sludge. At the core of the CLR Process is the horizontal Magna Rotor, which sustains a high population of micro-organisms in the reactor to provide simple process control.
The Magna Rotor provides precise oxygen input into the biological process through adjustment of rotor immersion by raising or lowering the level control weir and by adjusting the rotational speed.
Maintaining a stable population of biomass
As ESI’s Mike Falkner, Civil Engineer – Principal explains, the wastewater facility at the University of Mississippi is different in several ways. He added: “Influent flows at the Wastewater Treatment Facility can therefore range from a low of 0.3-0.4 MGD to an average of 0.6-0.7 MGD – to a high of 1.2 MGD. This creates those significant operational challenges in trying to maintain a stable population of biomass within the treatment reactor, which is a biological treatment process.
Faced with a growth rate that would overwhelm existing wastewater facilities as early as 2017 – and experience periods of overload prior to that, the University sought the most feasible approach – from economic, environmental and social perspectives, for the next 20 years.
ESI saw that whilst the existing system’s water conservation effort had been beneficial in many respects, it had placed higher demands on the WWTF, especially when trying to consistently meet the discharge limit for ammonia nitrogen of 2 mg/l.
However, the negative impacts related to this alternative were considered far greater – particularly the City of Oxford’s commercial usage rates for treating wastewater – but the fact that it would leave the University vulnerable to future rate increases. Charges would also apply to maintenance, expansion and replacement of its existing collection system components.
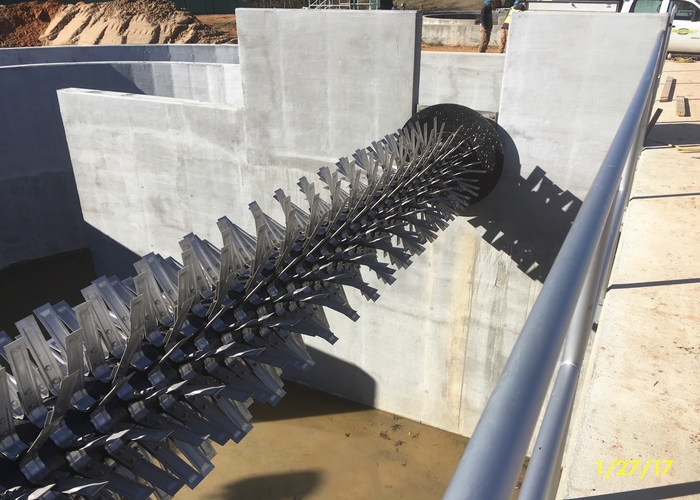
ESI proposed the introduction of a second Lakeside oxidation ditch, as well as the addition of anoxic tanks upstream of both ditches for enhanced biological nutrient removal (BNR) to help maintain compliance with more stringent National Pollutant Discharge Elimination System (NPDES) discharge limits.
The proposed new process train would have to be slightly higher in capacity than the existing ditch, and new headworks would be constructed to optimize the flow balance between the two. Other components would also have to be modified to handle pumping, sludge treatment and chemical treatment.
The most beneficial aspect of this alternative is that the University retains full control of wastewater treatment/disposal activities. Any decisions which would increase operational costs would be made by the University instead of the City, where the University has no vested representation.
The annual debt service plus operational cost of this expansion would be substantially lower over the life of the facility than either option involving off-campus treatment. The initial capital cost was higher than the other options and the WWTF would still be located next to the prestigious Stadium – but the visual and odor related social impacts would be attenuated by the use of covers and air scrubbers.
Very easy to maintain
Mike Falkner continued, “The most recent project added a third clarifier, new screening and grit removal systems, a headworks odor control scrubbing system, and an aerobic sludge digestor as well as an ultraviolet disinfection system. This included Lakeside’s Grit Removal system, the SpiraGrit, which has no submerged bearings, so is very easy to maintain”.
Compact in design, this system consistently removes inorganic grit from the treatment plant in a mechanically induced vortex environment. The efficiently removes grit over a wide range of daily flow rates. Rotating paddles maintain the flow velocity in the vortex chamber, keeping organics in suspension while allowing heavier grit to settle on the chamber floor. The settled grit moves across the floor and falls into the lower grit hopper.
Lakeside also supplied its Raptor® Micro Strainer, which captures small debris that passes through other screens. The captured screenings are washed, compacted, and dewatered to a dry solids content of 40 percent as they are transported up the inclined screw for disposal. This step reduces the volume by 50 percent and weight by 67 percent, ultimately reducing disposal costs.
“Again, this is a simple yet very effective design with a single drive that keeps maintenance costs low for the University”, said Mike Falkner.
“The University’s popularity and growth was underlined in the Fall of 2016 when enrolment reached an all-time high of 24,250 students. Overall, enrolment has grown by a massive 40.5% over the past decade, and by 13.1% in the past five years alone – so putting all of these futureproof measures in place has been crucial.
Much more energy-efficient
The current configuration now has a flow capacity of 1.5 MGD with a peak of 2 MGD. It is designed to be highly energy efficient because the aerators in the ditches are controlled based on dissolved oxygen levels in the mixed liquor using variable frequency drives. This means that they only inject as much oxygen and mixing as necessary to maintain high quality effluent. This is much more energy-efficient that timers or other mixing schemes since it is based on real time operational conditions”.
Investing in Lakeside’s robust engineering was very much part of our commitment to the long-term wellbeing of the University of Mississippi’s wastewater treatment facility. It is tough, reliable equipment, which requires only basic maintenance,” he concluded.