SIDE INDUSTRIE, a family company specialized for 30 years in solutions for the pumping of difficult fluids, invented a new clean and safe way on how to lift raw effluents through the concept of Direct In-Line pumping with no wet well, also called wastewater circulation, patented and called DIP Systeme®.
Based on practical expertise in the field, the development of our product range is the result of 35 years of research, and from listening to the daily concerns of users and designers, enabling us today to offer innovative solutions which are both simple and complete. Many are already standard use in Europe for several years now.
By lifting gravity effluent directly at the point of entry, without water loading or a wet well, the DIP SYSTEME® overcomes the drawbacks of retained volumes of effluent such as: dangerous gases (H2S), odors, sand and grease accumulation, equipment corrosion, structural erosion, clogged floaters; and offers access safety.
The DIP SYSTEME® is then the ideal solution for communities that want to modernize or extend their wastewater collection networks as it makes it possible to design durable and economical pumping stations with no wet well . The absence of a collection tank eliminates costly cleaning operations of traditional units and eliminates in the same time the complaints from residents living close to an installation that produces unpleasant odors and the risks for maintenance technicians.
The DIP Systeme® allows designing lift stations in small spaces and so enables civil engineering costs to be significantly reduced. A single equipment size can respond to multiple cases with the same construction.
In case of lift station rehabilitation, DIP settles down and adapts itself to all existing lift station forms. It allows to increase flow capacities or discharge pressure that became too weak, without engineering modifications.
A current wet well can be converted to a clean, dry DIP Systeme® lift station without the expense of the corrosion resistant materials. Or as part of a new lifting station installation project, the DIP Systeme® enables engineering costs to be significantly reduced: Site work requires, at least, 1 meter (3 feet) less in foundation depth and concrete, and takes up less space than a traditional station.
The structure’s shape can be either round or square and commercially available ducting and pipes prefabricated in concrete are more than adequate to contain the DIP equipment and the valve systems. Dry installation enables the single gate valve and check valve to be assembled in the same location as the DIP Systeme® without the need for a separate valve chamber.
A single hatch is required. For inlet levels which are not very deep, the equipment room can even be constructed out of concrete blocks as there is no “pit” to be flooded, and it is therefore watertight. During station renovation: The DIP Systeme® adapts to any type of currently available pipework; so precise positioning of input/output pipes is no longer required. The discharge head can be positioned at any angle through 360.°
The problem with rehabilitation is the downtime… When the flow cannot be stopped or bypassed easily, the DIP design and its accessories permit transforming the existing lift station in 5 steps without downtime in less than 2 hours.
The DIP can be installed above the existing pumps while still operating; LET’S SEE THE STEPS:
- Use pipeplug upstream. Install the wall flange + the knife valve open (downtime : 1hr) Then release the flow.
- It is now possible to control the flow with the knife valve.
- Install the DIP with the stone trap open. The flow can go through! (downtime : 1hr) Then release the flow.
- Connect the discharge pipe to one of the existing pump gate valves. Connect one DIP unit to the supply power even in direct start. (downtime : 2hr)
- Ready to switch! A last deep cleaning, fill up the bottom with concrete or resin floor, do not forget a pit for the sump pump, and that’s it.
The existing pump system keeps operating until the last switch. Hundreds of wet well stations have been transformed to a clean, dry & safe DIP room this way, and saved money.
Here are some examples of rehabilitation made with different DIP systems in different countries all around the world …
SEPTA (Southeastern Pennsylvania Transportation Authority) chose and ordered via our distributor in Pennsylvany, USA, Robert Brown Associates, Inc. our products DomoDIP® and DipCut® to rehabilitate their wastewater pumping station at Lansdowne station.
The main asset of our DomoDIP is that it is a direct in line pumping system totally safe and clean with No wet well so No more odor ! Combined with our DipCut technology this pump system is the best solution to clogging problem and this is why SEPTA did chose our technology. After the success if this first installation at Lansdowne station, SEPTA installed 4 other DomoDIPs for similar cases in different stations.
In the countries with hot climate we have to face the same problems : the lack of drinking water and too long retention time in sanitation causing problems such as odors and emanation of H2S.
In 2015, in Ivory Coast, the DIP Systeme technology has been chosen for the rehabilitation of this lift station in St Jacques because it allows the reduction of retention time and the aeration of the effluent while pumping in order to fight against H2S.
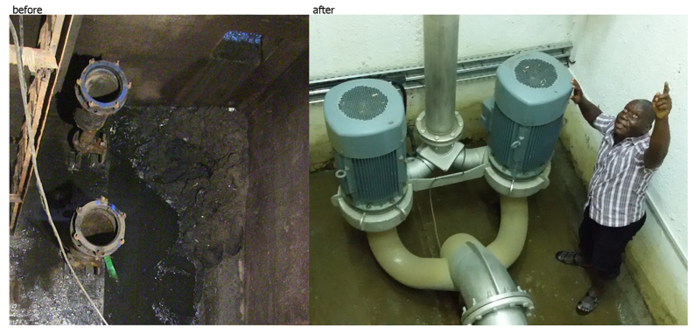
The PUIUR (Projet d’Urgence d’Infrastructures Urbaines) did then choose to rehabilitate the St Jacques lift station by replacing 3 submersible electro-pumps groups by only one DIP 151 / 4VV – 55 kW (75HP) designed for a flow of 400 m3/h (1761 gpm) at 42 m (138 ft) of head for each pump. The DIP System has been installed by the company Águas em Processo, S.A. and is operated by Sodeci.
In 2011, the company Águas em Processo, S.A. has been commissioned by Águas do Centro Litoral for the rehabilitation of the pumping station of Fontainhas. Indeed this lift station was initially equiped with 3 submersibles pumps but showed operational problems causing odors troubles and weekly cloggings.
After replacing those 3 pumps by only one DIP 151 / 4VV-45 Kw (designed for a low of 300 m3/h (1320 gpm) at 42m (137 ft) of head) this lift station now operates at full capacity without any trouble and Águas do Centro Litoral noticed as well a large decrease on operational costs.